Magnetic Particle Testing
Magnetic Particle Testing (MPT): Detecting Surface and Near-Surface Discontinuities in Ferromagnetic Materials

About
Magnetic particle testing or MPT is a nondestructive testing method for locating surface and near surface discontinuities in ferromagnetic materials. It depends for its operation on the fact that when the material or part under test is magnetized, discontinuities that lie in a cause leakage field to the direction of the magnetic field will cause a leakage field to be formed at and above the surface of the part. The presence of this leakage field, and therefore the presence of the discontinuity, is detected by the use of finely divided ferromagnetic particle applied over the surface, some of the particle being gathered and held by the leakage field. This magnetically held collection of particle forms an outline of the discontinuity and generally indicates its location, size, shape and extent. Magnetic particles are applied over a surface as dry particles, or as wet particle in a liquid. Ferromagnetic materials include most of the iron, nickel and cobalt alloys. These materials lose their ferromagnetic properties above a characteristic temperature called the Curie point which is approximately 760◦ C for most of the ferromagnetic material.
Ultrasonic Testing
The principal industrial uses of magnetic article testing are final inspection, receiving inspection, in process inspection and quality control, maintenance and overhaul in the transportation industries, plant and machinery maintenance and inspection of large components.
Applicability
Limitations
● Magnetic particle inspection methods will work only on ferromagnetic materials
● Post cleaning to remove remnants of the magnetic particle clinging to the surface may be required after testing and demagnetization
● Demagnetization following magnetic particle testing is often necessary
● Exceedingly large currents sometimes are required for very large parts
● Care is necessary to avoid local heating and burning of finished parts or surface at the points of electric contact
● Although magnetic particle indications are easily seen, experience and skill in interpreting their significance are needed
● The magnetic field must be in a direction that will intercept the principle plane of the discontinuity
Some of Our Clients!










Magnetic Particle Testing
Magnetic Particle Testing (MPT) is a nondestructive method used to detect surface and near-surface defects in ferromagnetic materials like iron, nickel, and cobalt alloys. When magnetized, discontinuities create leakage fields that attract fine magnetic particles, forming visible patterns indicating the defect’s location and size. These particles can be applied in dry or wet forms. The process is effective until materials reach their Curie point, around 760°C.
- MPT detects surface and near-surface defects in ferromagnetic materials.
- Magnetized materials with discontinuities produce leakage fields.
- Fine magnetic particles highlight these fields, revealing defect patterns.
- Particles are applied dry or suspended in liquid.
- Ferromagnetic properties are lost above the Curie point (~760°C).
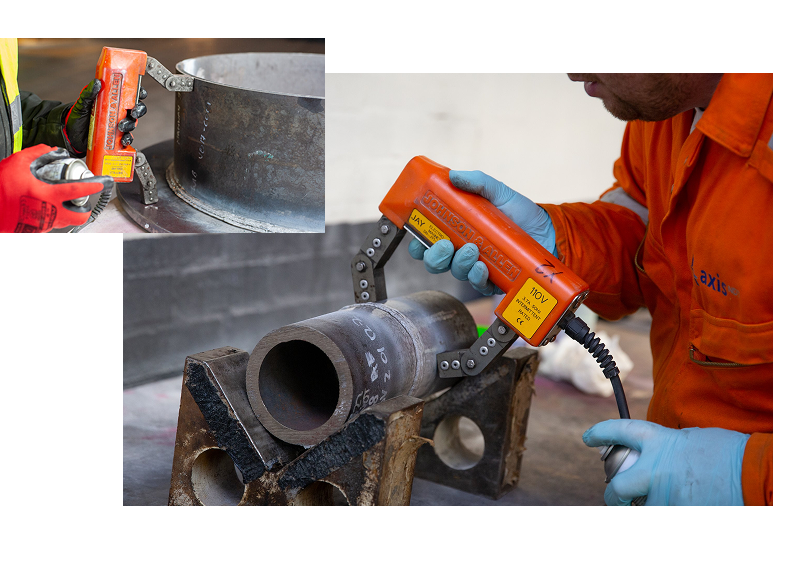
Magnetic Particle Testing
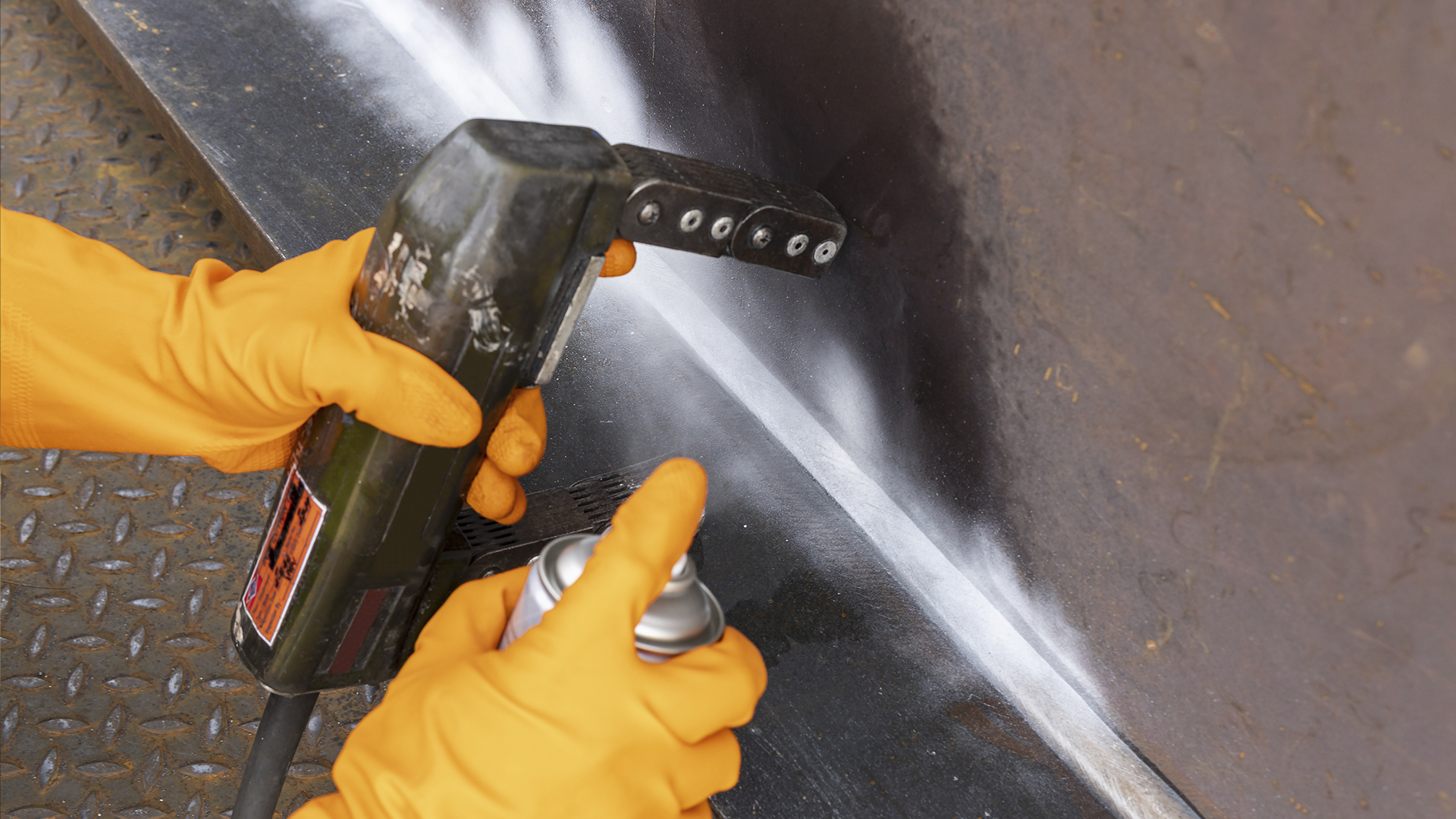

Applications
The principal industrial uses of magnetic article testing are final inspection, receiving inspection, in process inspection and quality control, maintenance and overhaul in the transportation industries, plant and machinery maintenance and inspection of large components.
- Used to inspect engine components, gears, and suspension parts for cracks or defects.
- Helps detect flaws in turbine blades, landing gear, and structural parts.
Limitations
Magnetic particle inspection methods will work only on ferromagnetic materials.
For best results, the magnetic field must be in a direction that will intercept the principle plane of the discontinuity. Sometimes this requires two or more sequential inspections. With different magnetizations.
Demagnetization following magnetic particle testing is often necessary.
Post cleaning to remove remnants of the magnetic particle clinging to the surface may be required after testing and demagnetization.
Exceedingly large currents sometimes are required for very large parts.
Radiography cannot detect laminations due to their unfavorable orientation.

Applications
The principal industrial uses of magnetic article testing are final inspection, receiving inspection, in process inspection and quality control, maintenance and overhaul in the transportation industries, plant and machinery maintenance and inspection of large components.
Limitations

Magnetic particle inspection methods will work only on ferromagnetic materials.

For best results, the magnetic field must be in a direction that will intercept the principle plane of the discontinuity. Sometimes this requires two or more sequential inspections. With different magnetizations.

Demagnetization following magnetic particle testing is often necessary.

Post cleaning to remove remnants of the magnetic particle clinging to the surface may be required after testing and demagnetization.

Exceedingly large currents sometimes are required for very large parts.

Care is necessary to avoid local heating and burning of finished parts or surface at the points of electric contact.

Although magnetic particle indications are easily seen, experience and skill in interpreting their significance are needed.
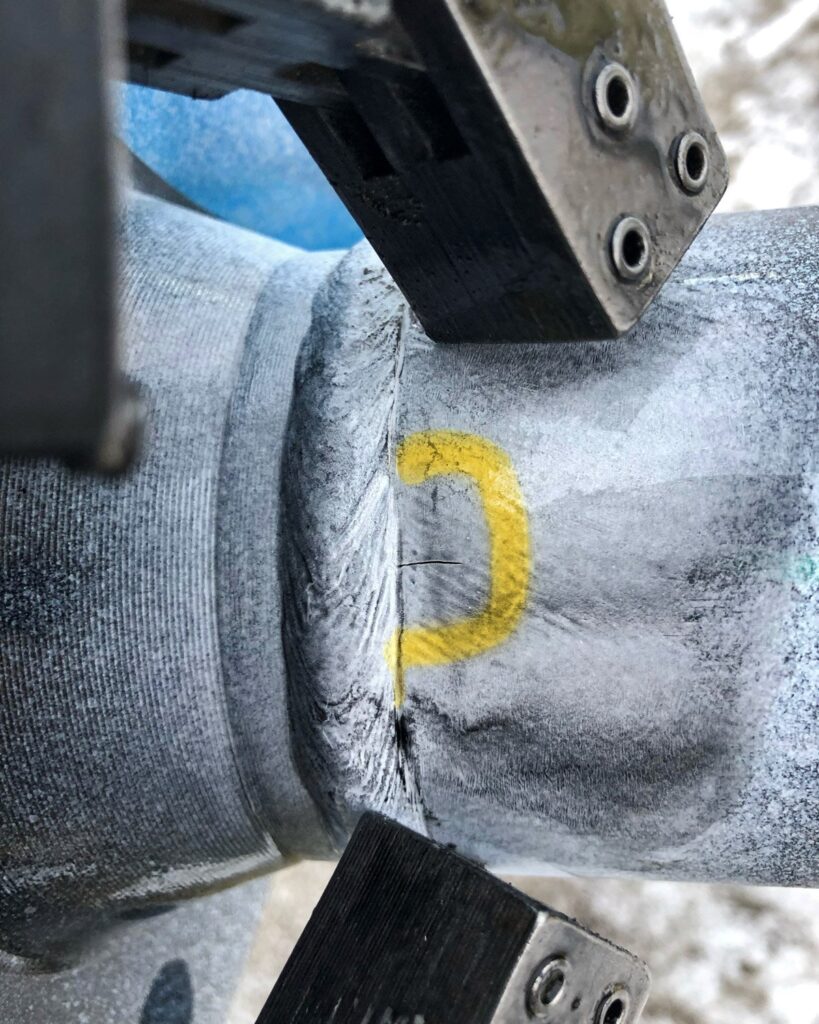
Why Choose Us for Magnetic Particle Testing
- Highly sensitive for detecting surface and near-surface defects
- Cost-effective with minimal preparation requirements
- Provides real-time inspection results
- Portable and suitable for on-site testing
- Non-destructive, preserving the integrity of components
- Effective for complex defect detection like cracks and seams
1
Highly Sensitive
2
Cost-Effective
3
Real-Time Results
LPT is often more sensitive for detecting fine surface defects in non-ferromagnetic materials, whereas Magnetic Particle Testing is limited to ferromagnetic materials.